Home | VOC recovery units
Why wasting “ cold energy “ to the environment to vaporize liquid nitrogen and not use it profitably?
Modern solutions, Cryogenic
Low temperature and cryogenic condensation is a process that can be used as an effective means for VOC emissions control.
Cryogenic condensation technology is based on lowering the vapor pressure of a component by reducing the temperature of the process stream thus increasing the recovery of the components in the liquid or solid phase.
Nitrogen gas is widely used in the process industry, it is inert and is usually transported and stored in a liquid state at low temperature and medium pressure. Liquid nitrogen is a convenient medium to use, its low temperature cooling capacity allows the design of highly efficient condensing systems.
- Solvent Recovery Unit
- Recovery of chemicals and Petrol Vapor
The Need
PraxEidos has developed technology to remove volatile organic compounds (VOCs).
The aim is to reduce the damage that VOCs cause to human health and environment.
Many of these substances are carcinogenic and cause photochemical smog.
The neatest and cleanest way to remove VOCs from exhaust gas stream is condensation with liquid nitrogen.
The technology from PraxEidos removes VOCs to meet emission level lower than 20 mg/Nm3, as well as overcoming the limitations of traditional control methods.
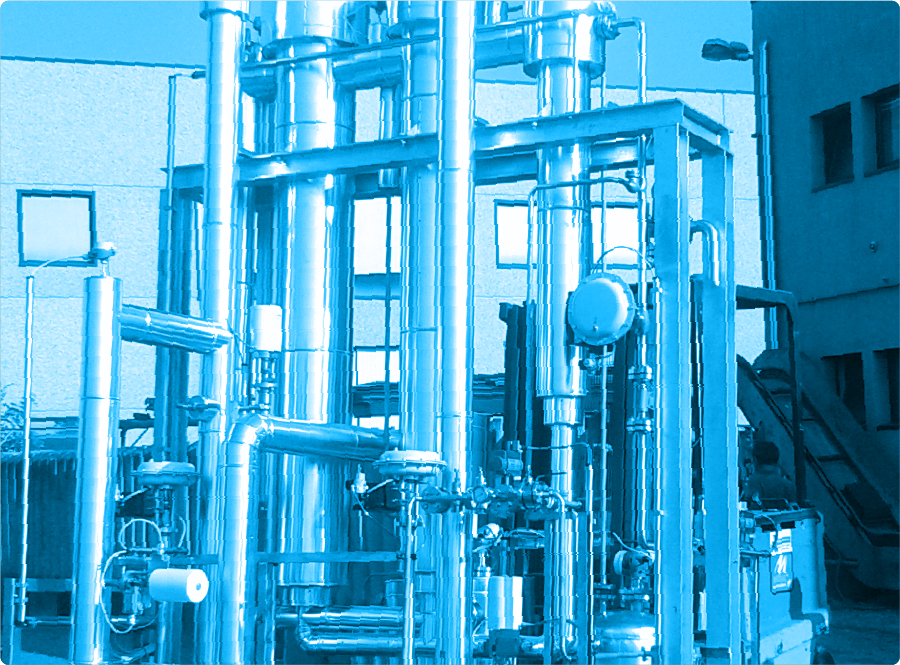
The Technology Provided
A responsible approach towards protecting the environment means limiting the emissions of volatile components.
One method is the condensation of these components by cooling the exhaust stream with liquid nitrogen.
As the vapours are getting cooled, the volatile components condense and freeze. These solid particles can be trapped, leaving a clean stream of gas to be vented to the atmosphere.
The understanding of the heat transfer mechanism has promoted special heat exchanger geometries which are best suited to the properties of boiling nitrogen and condensation of Vocs within incondensable vapours.
The temperature required to meet acceptable emission standards (in the order of tens parts per million (ppm)) are typically -150 °C and lower.
The obvious choice of cooling medium is liquid nitrogen, which can provide the cooling down to -180 °C.
The design of the heat exchangers poses a special challenge which is beyond the typical heat exchanger design packages.
Not only there are temperatures outside the normal parameters, but the heat transfer relationships must to consider the nitrogen boiling and heating, and the condensation and freezing of multiple volatile components in an incondensable stream.
PraxEidos has developed computer design tools to model these heat transfer mechanism and generate valid heat exchanger designs.
The Benefit
The Cryogenic recovery system, designed and supplied by PraxEidos, combines the refrigeration power of liquid nitrogen with the inerting property of gas nitrogen, resulting in a skid mounted VOCs control system that is simple to install, economical and effective.
Running costs are reduced to a minimum by the ability to reuse the nitrogen to purge and blanket pipe work and tanks.
Recovered VOCs can often be reused directly – something that is more difficult with carbon bed technology and impossible with incinerators and catalytic oxidisers.
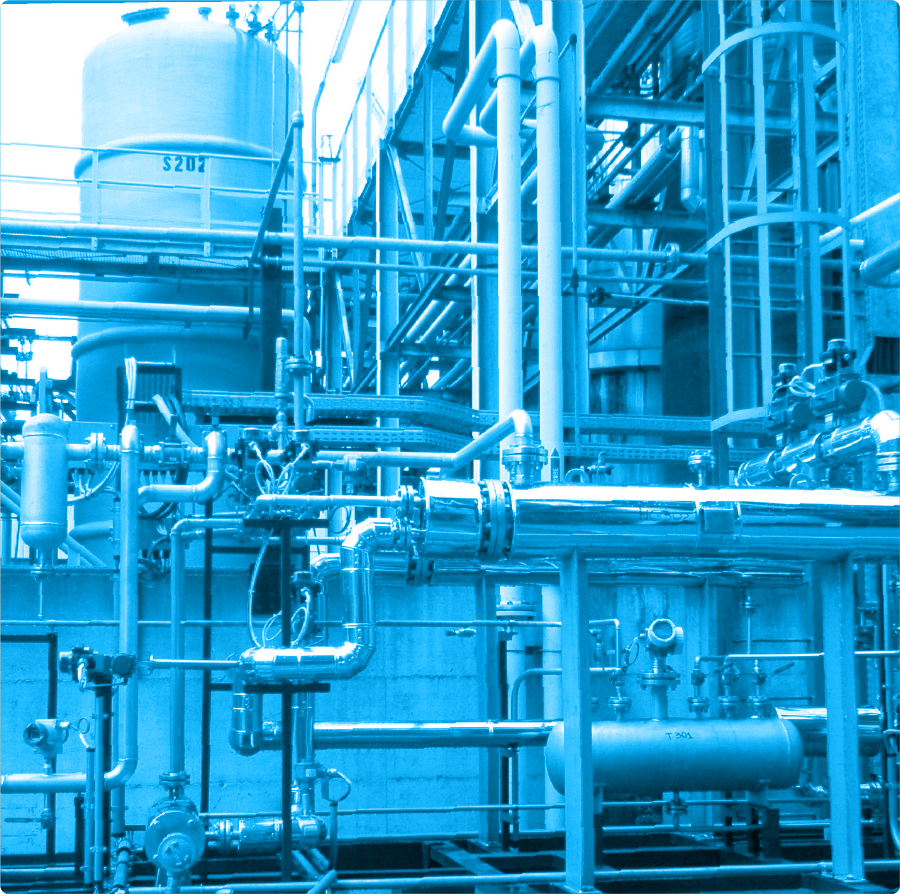
During filling operation of road and ship tankers
a) The Need
The refueling of chemical tankers and ships involves a large emission of highly polluting vapors into the environment in addition, valuable product that can be recovered and resold is expelled.
In addition valuable product is vented. It can be recovered and resold.
b) Quantifying the problem
The “empty “ road and ship tankers after the discharging operations are in fact full of vapors : a mixture of air and petrol or chemicals products.
Refilling fresh liquid petrol leads to venting of the vapor to the environment.
c) Recovering the petrol vapor, the technology:
The easiest way to recover the petrol or chemicals products vapor is the cryogenic condensation.
Vapors are collected from the filling points and transported in a dedicated pipe to the condensation unit.
An extraction blower allows for the control of the flow rate in the range of 0 – 100% of the condensation unit capacity .
d) Direct expansion of liquid nitrogen
The vapor mixture is cooled by means of boiling of liquid nitrogen in a special designed heat exchanger.
The boiling temperature of liquid nitrogen at ambient pressure is -196 °C.
The process gas can be cooled at a very low temperature, allowing to keep the most stringent emission limits prescribed by the law.
Ship Application
Final volatile organic compound concentration at the end of purging operation: <150 mg/Nmc
Tipical products to be recovered
- Ethylene
- Propane
- Propylene
- Methane + Ethane
- Butene-1
- i-Butylene
- Butene-2
- n-Butane + i-Butane
- Butadiene 1,3
- Isobutane
- n-Butane
- Isobutylene
Benefits
- Residual concentration of petrol or chemicals product vapor
- to the environment < 5 grams/m3
- Specific liquid nitrogen 1.5 Kg /Kg recovered petrol
- Recovery of gas nitrogen for the facility needs
Limit
- Cost and availability of liquid Nitrogen
Recovered products
- Pure liquid petrol – It can be reused as it is
- The quantity is 90% of the incoming vapor phase
Standard flow chart
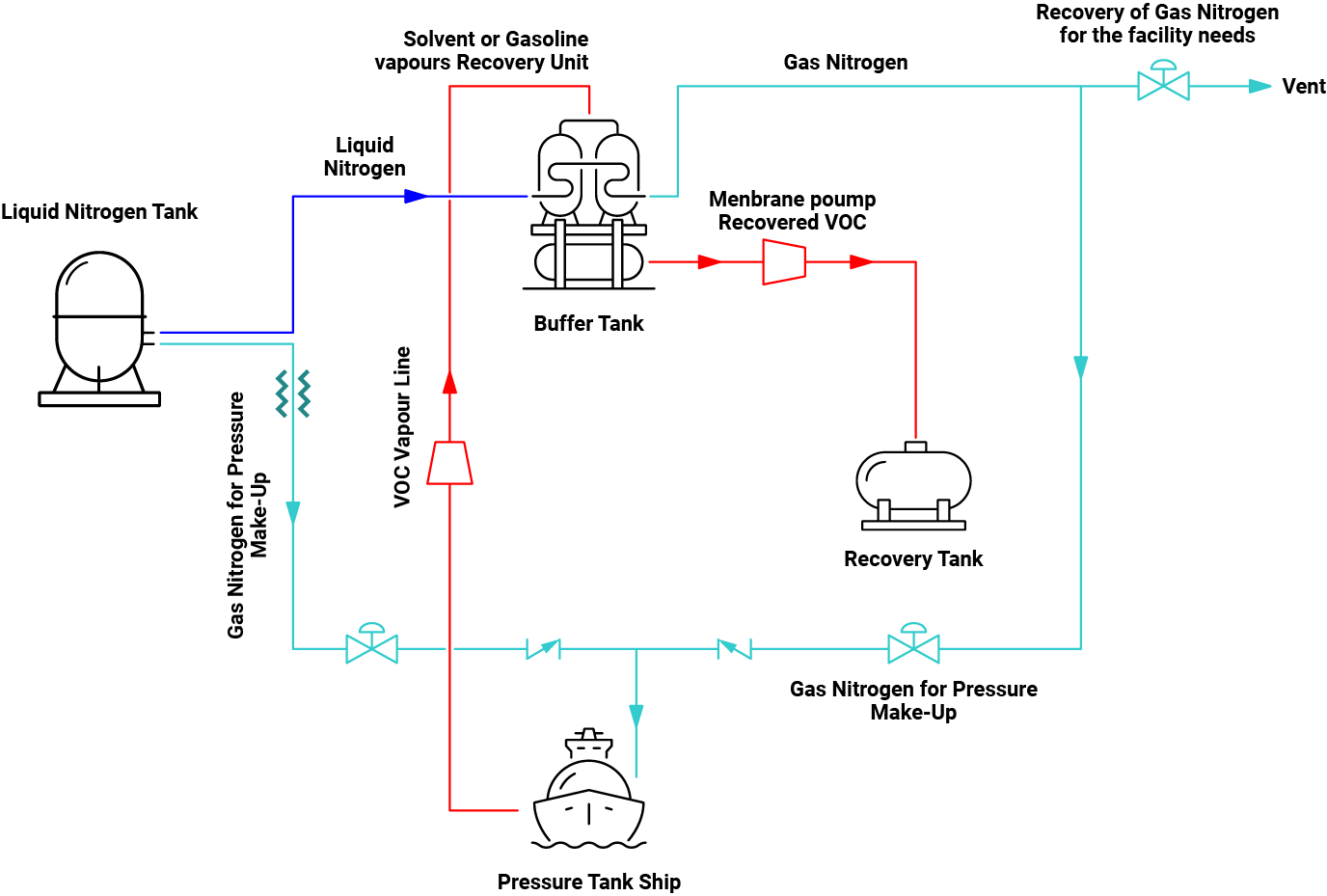